Product
Recommended article
- Taming Dust Pollution with the Dust Monitoring System
- The All - in - One Grassland Ecological Monitoring Station (FT - CQX9)
- Combatting Dust Pollution: The Pivotal Role of Cruise Monitoring System
- On - the - Go Meteorology: Unraveling the Power of Vehicle - Mount Weather Stations
- The Crucial Link: Photovoltaic Weather Station and Efficient PV Generation
- Monitoring Forest Litter Moisture Content
Contact us
Shandong Fengtu IOT Technology Co., Ltd
Sales Manager:Ms. Emily Wang
Cel,Whatsapp,Wechat:+86 15898932201
Email:info@fengtutec.com
Add:No. 155 Optoelectronic Industry Accelerator, Gaoxin District, Weifang, Shandong, China
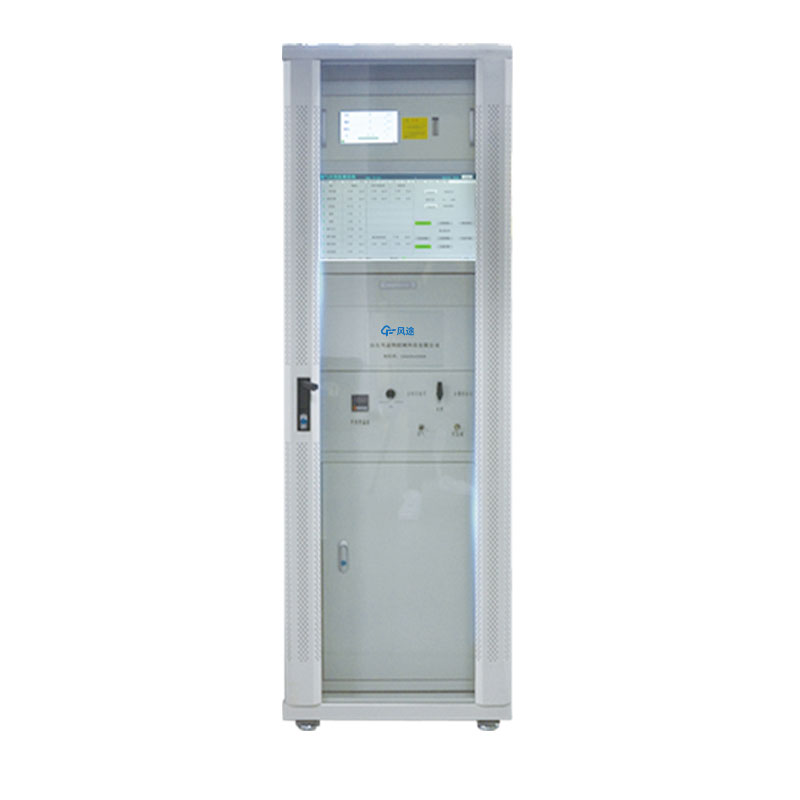
Online CEMS Gas Analyzer
Model:FT-CEMS-B
Brand:fengtu
Related products
1.Online CEMS Gas Analyzer Project Introduction
Online CEMS Gas Analyzer Online monitoring of SO2, NOx, O2 emissions, flue gas parameters (temperature, pressure, flow rate, humidity) and soot from various stationary sources.The Online CEMS Gas Analyzer launched by Fengtu Technology can continuously monitor SO2, NOX, 02 (standard, wet basis, dry basis and converted), particulate matter concentration, flue gas temperature, pressure, flow rate and other related parameters, and calculate emission rate, total emission, etc., so as to effectively manage the measured data.
Online CEMS Gas Analyzer consists of four mandatory subsystems: gaseous pollutant (SO2, NOX, O2, etc.) monitoring, particulate matter monitoring, flue gas parameter (temperature, pressure, flow rate, etc.) monitoring, and data acquisition and processing.
Gaseous pollutant monitoring adopts the extractive condensation method + phosphoric acid titration pretreatment. The principle is to use the ultraviolet differential method to measure the SO2 and NOX content in the flue gas, measure the wet oxygen content by the electrochemical method, and then calculate the dry flue gas concentration of SO2, NOX, and 02 by dry-wet conversion. Phosphoric acid titration pretreatment can effectively reduce the adsorption loss of SO2 during condensation and water removal, and improve the measurement accuracy.
Particle monitoring adopts the extraction measurement method, the flue gas temperature is measured by a temperature sensor, the flue gas pressure is measured by a pressure sensor, and the flue gas flow rate is measured by a Pitot tube; all measurement signals are sent to the data acquisition and processing system.
The output processing system has the functions of real-time transmission of field data, remote fault diagnosis, report statistics and graphic data analysis, realizing unattended work on site. The whole system has a simple structure, wide dynamic range, strong real-time performance, flexible networking and low operating cost. At the same time, the system adopts a modular structure, which is easy to combine and can fully meet the requirements of communication with the DCS system within the enterprise and the data system of the environmental protection department.
000011 Project Implementation Standards
The design, manufacture and acceptance of this system are mainly carried out in accordance with the following standards and technical specifications:
u GB3095-1996 "Air Environment Quality Standard"
u GB13223-2003 "Emission Standards of Air Pollutants from Thermal Power Plants"
u GB18485-2007 "Standards for Control of Pollutants from Incineration of Domestic Waste"
u HJ/T75-2007 Technical Specifications for Continuous Monitoring of Flue Gas Emissions in Thermal Power Plants
u CJJ90—2002 Technical Specifications for Urban Domestic Waste Incineration Engineering
u CJ/T118—2002 Technical Specifications for Municipal Solid Waste Incinerators
u HJ/T76-2007 Technical Requirements and Detection Methods for Continuous Monitoring System of Flue Gas Emissions from Stationary Pollution Sources
u GB16297-1996 Comprehensive Emission Standards for Air Pollutants
GB/T16157-1996 "Determination of particulate matter in exhaust gas from solid pollution sources and sampling methods for gaseous pollutants"
u GB9078-1996 Comprehensive Emission Standards of Air Pollutants from Industrial Furnaces
u GB 3095-1996 "Ambient Air Quality Standard"
u GB12519-1990 "General Technical Requirements for Analytical Instruments"
000012 Project Plan
000012.1 Measurement items
ØSO2, NOX, O2, smoke, temperature, pressure, flow rate
000012.2 Measurement method
ØFlue gas sampling method: Extractive condensation method
ØSO2, NOX monitoring method: Differential optical absorption spectroscopy (phosphoric acid titration pretreatment)
ØO2 monitoring method: electrochemical method
ØSmoke measurement method: Extraction measurement method
ØTemperature measurement method: temperature sensor
ØPressure measurement method: pressure sensor
ØFlow rate measurement method: differential pressure method (Pitot tube)
2. Online CEMS Gas Analyzer System General Principles
The technical requirements of the functional design, structure, performance, installation and testing of the system equipment are in line with the relevant national environmental protection standards and meet the standards of the environmental protection industry of the People's Republic of China (HJ/T75-2007, HJ/T76-2007).
Our company's CEMS system consists of a gaseous pollutant monitoring subsystem, a particulate matter monitoring subsystem, a flue gas parameter monitoring subsystem, and a data acquisition and processing subsystem. The gaseous pollutant monitoring subsystem and the data acquisition and processing subsystem are installed in a standard 19-inch cabinet. The system composition is shown in the following figure:
Figure 1. CEMS system composition diagram
ØGaseous pollutant monitoring subsystem: consists of sampling unit, pretreatment unit and analysis unit.
ØParticle monitoring subsystem: using extraction type smoke monitor.
ØSmoke parameter monitoring subsystem: Pitot tube is used to measure flow rate, pressure sensor is used to measure pressure, temperature sensor is used to measure temperature, and high temperature capacitance humidity sensor is used to measure smoke humidity.
ØData acquisition and processing subsystem: consists of data collector, industrial computer, display and system software.
The above subsystems can be tailored according to different customer needs.
Figure 2. CEMS system installation diagram
3. System composition
3.1 Monitoring of gaseous pollutants
3.1.1 Sampling and pretreatment unit
The sample gas is taken out by the sampling probe under the suction force of the sampling pump. Most of the particulate matter in the sample gas is filtered out by the filter in the sampling probe, and then transported to the refrigeration system by the heating pipeline for condensation and dehydration, and then sent to the analysis unit for analysis. According to the characteristics of high humidity and low SO2 in ultra-low temperature systems, in order to reduce the adsorption loss of SO2, the pretreatment system adopts a relatively reliable and simple phosphoric acid titration method. More than 5% phosphoric acid solution is added to the condenser pretreatment, so that the condensed water is always in an acidic state, reducing the adsorption loss of SO2 and improving the measurement accuracy. The condensed water is discharged through the drainage system. The control unit realizes functions such as backflush, calibration, and refrigeration temperature alarm prompts, and displays various working states of the system.
The pretreatment system uses a first-stage rapid condensation to remove water to ensure that the gas composition remains unchanged. A second-stage fine filtration is used to ensure that the gas measurement chamber is not contaminated, thereby increasing the service life of the analyzer. The figure below is a flow chart of the gaseous pollutant monitoring system.
3.1.2 Gas analyzer
Instrument: UV spectrometer gas analyzer
Model: HM-UVA-100
Measurement principle: Differential Optical Absorption Spectroscopy (DOAS)
Measuring principle
The UV spectrometer gas analyzer is a gas analysis instrument based on multi-channel spectral analysis technology (OMA) and differential optical absorption spectroscopy technology (DOAS). The light beam emitted by the light source converges into the optical fiber, and is transmitted to the gas chamber through the optical fiber. After passing through the gas chamber, it is absorbed by the gas to be measured, and then transmitted to the spectrometer by the optical fiber. After grating spectroscopy inside the spectrometer, the array sensor converts the split light signal into an electrical signal to obtain the continuous absorption spectrum information of the gas. Based on this spectral information, the instrument uses the differential absorption spectroscopy algorithm (DOAS) and the partial least squares algorithm (PLS) to process and obtain the concentration of the measured gas.
ØMulti-band spectral analysis technology (OMA)
Since various gas molecules have different absorption of light waves in different bands, the simultaneous measurement of multiple gases can be achieved by analyzing the continuous spectrum after gas absorption.
The ultraviolet spectroscopic gas analyzer uses ultraviolet light sources and sensors to measure the concentration of gases that absorb light waves in the ultraviolet band, such as SO2, NO, NO2 and other gases.
ØDifferential Optical Absorption Spectroscopy (DOAS)
The core idea of DOAS is to decompose the absorption spectrum of gas into two parts: fast-changing and slow-changing. The fast-changing part is related to the structure of gas molecules and the elements they are composed of, and is the characteristic part of the absorption spectrum of gas molecules; the slow-changing part is related to the interference of smoke, water vapor, background gas, and changes in the measurement system, and is the interference part. DOAS uses the fast-changing part to calculate the concentration of the measured gas, and the measurement results are not interfered with and have high accuracy.
The UV spectrum gas analyzer adopts a unique processing method that combines the DOAS algorithm and the PLS algorithm to eliminate the interference of smoke, water vapor, and background gas. It also eliminates the influence of measurement system fluctuations on the measurement results, ensuring the accuracy and stability of the measurement.
Technical indicators
SO2: 0~20~100ppm (can be customized according to buyer's needs)
NO: 0~20~100ppm (can be customized according to buyer's needs)
Accuracy: ≤±2%
Linear error: ≤±2%FS
Zero drift: ≤±2%FS/7D
Range drift: ≤±2%FS/7D
Response time: ≤30s
other
O2 measurement electrochemical, 0~25%, ≤±2%FS
Power supply: 220VAC, 50Hz
Ambient temperature limit: -10~40℃
Communication interface: 1 RS232; 1 RS485/RS232
Digital interface: 4 relay outputs, 2 binary inputs
Analog interface: 5-way 4~20mA output, 2-way 4~20mA input
Instrument features
ØHigh reliability
It uses a pulse xenon lamp with a service life of 10 years as the light source and a solidification spectrometer, with no moving parts and high reliability.
ØCombined gas chamber design
The combined gas chamber design makes spectrum adjustment easy and improves spectrum intensity.
ØHigh measurement accuracy and good stability
Using DOAS (Differential Optical Absorption Spectroscopy) algorithm, the measurement results are not affected by factors such as smoke, dust, moisture, etc., and the measurement accuracy is high; at the same time, the DOAS algorithm also eliminates the errors caused by instrument aging, and the measurement stability is good.
ØHighly intelligent and digital
It has multiple high-performance processors built in, and the processors use high-speed data bus communication technology. Each module has powerful digital configuration and detection functions; it is simple to operate and easy to use.
ØRich user interface
Provides a variety of interfaces, can be easily integrated into various control and monitoring systems. Through RS485 and RS232 and other communication methods to build a wireless or wired network, to facilitate the daily operation, maintenance and management of the instrument.
ØComparison with common analyzers
category | HM-UVA-100 | Non-dispersive infrared (NDIR) |
Spectral range | Holographic grating spectrometer, diode array detector, complete continuous absorption spectrum | Non-spectral, bandpass filter, measuring absorption at characteristic wavelengths |
Wavelength resolution | High, 0.6nm | Low, 20-30nm |
Linear response | High wavelength resolution ensures linear response | Large filter passband width results in nonlinear response to gas concentration |
Measurement dynamic range | Large, suitable for simultaneous measurement before and after desulfurization | Small |
Effect of flue gas humidity | Not affected by smoke humidity | Humidity and filter components affect calibration results |
Calibration cycle | Wide continuous spectrum, high wavelength resolution, long calibration period | Short calibration cycle |
Anti-interference ability | Strong, wide continuous spectrum and high wavelength resolution eliminate interference from particles, moisture and background gases | Weak, particularly susceptible to moisture interference |
reliability | No moving parts inside, good reliability | There are moving parts such as choppers, which affect operational reliability |
Online CEMS Gas Analyzer3.1.3 Analysis System
The analysis system consists of:
ØSampling unit (probe, filter, thermostat);
The sampling unit of the FT-CEMS-B system is mainly composed of a sampling probe and a heating pipeline. The sampling probe is installed at an appropriate position of the flue (or chimney) in accordance with national standards to collect the gas in the flue and transport the gas to the heating box inside the cabinet through the heating pipeline. To ensure the accuracy of the measurement results, the sampling probe and the heating pipeline are both electrically heated, which can keep the gas at a set temperature to prevent condensation of moisture in the gas. The length of the heating pipeline can be customized according to the actual needs of the buyer.
ØPretreatment unit (sampling pump, dehumidification, fine filtration, drainage, etc.);
The flue gas reaches the pretreatment system through the high-temperature sampling probe and the heating pipe. The pretreatment system switches to the condenser through the sampling ball valve for steam-water separation. The condensed water is discharged in time through the peristaltic pump, condensed and dehydrated by the condenser, and then dust-removed and filtered through the three-stage fine filter. The clean, dust-free and water-free sample gas after treatment enters the flue gas analyzer for analysis and measurement.
ØAnalytical unit (SO2, NO, NO2, O2);
ØSignal output (SO2, NO, NO2, O2 concentration, range conversion, calibration status, fault status, etc.);
ØOthers (gas circuit, circuit, etc.);
ØAnalytical instrument cabinet: 1800×530×730MM (height*depth*width).
3.2 Particle monitoring
Instrument: Extraction type smoke (dust) measuring instrument
Model: LFS1000-MO
Measuring principle: Laser extraction
Technical parameter table:
How it works | Laser forward scattering measurement principle |
Measurement object | Industrial waste gas, smoke |
Mechanical properties | Host shell: full metal shell |
Host size: 1670×750×600 mm (H×W×D) | |
Weight: Approx. 120Kg | |
Protection level: system IP55, electronic components IP65 | |
Optical properties | Working wavelength (650±20)nm |
Measuring performance | Measuring range: Dual range automatic switching, minimum (0-5) mg/m3 maximum (0-200) mg/m3 |
Zero drift: ±2%FS/24h Range drift: ±2%FS/24h | |
Indication error: ±2%FS | |
Detection limit: 0.01mg/m³ Flue diameter: (0.3~20) meters | |
Measurement conditions | Flue flow velocity: (0~30) m/s; Flue pressure: -5Kpa~5Kpa Flue gas temperature: Maximum 300°C Flue gas humidity: 30mg/m3 Anti-blocking backflush: Automatic, backflush time interval can be set |
Host power supply requirements | Voltage 220VAC, Power 3KW |
Work Environment | Working temperature: -20℃~+50℃ |
Interface Characteristics | Analog output: (4~20)mA |
Digital interface: RS485 |
Implementation standard: HJ/T 76-2007 Technical requirements and detection methods for continuous monitoring system of flue gas emissions from fixed pollution sources.
Product performance characteristics:
The integrated probe for speed measurement and sampling at the same point is adopted to support accurate isokinetic sampling.
Supports simultaneous output of four parameters: flue temperature, flue pressure, flue flow rate, and flue concentration.
The instrument adopts a variety of advanced technologies, including: correlation noise cancellation technology, laser emission power stabilization technology, extremely low noise TIA, interference control and signal integrity design, and anti-harsh environment design technology, to provide fast, reliable and accurate quantitative smoke emission data.
Unique patented automatic calibration technology realizes automatic calibration of zero and full scale. The system automatically performs zero and full scale calibration every 24 hours. It also supports manual zero calibration and automatic zero calibration.
The jet technology is used to extract part of the flue gas from the flue. It has a compact structure, simple installation, resistance to lightning strikes, resistance to harsh environments, low cost and low maintenance.
The flue gas sampling and transmission process is continuously heated and kept at a constant temperature to prevent measurement errors caused by condensation of wet flue gas during the transmission process.
It adopts intelligent technology and has display function, which can display various test data and fault prompts in real time, making it convenient for on-site debugging and maintenance.
Unique equipment operation status prompts, temperature abnormalities, and parameter abnormalities prompts.
Power-off self-protection function: after power failure, the backup battery is used to supply power, close the valve and protect the internal structure.
3.3 Flue gas parameter monitoring
3.3.1 Temperature, pressure and flow integrated probe (temperature, pressure and flow rate)
The structure of the temperature-pressure-flow integrated probe measurement device mainly includes micro differential pressure transmitter, static pressure sensor, thermal resistor (or thermocouple), pitot tube, back-blowing solenoid valve, temperature and pressure compensation, etc. Its measurement principle is: the primary pressure taking element adopts the traditional pitot tube measurement method. After correct installation, the full pressure and back pressure taking tubes of the pitot tube will transmit the detected dynamic pressure and static pressure to the differential pressure transmitter respectively. The differential pressure transmitter converts the difference between dynamic pressure and static pressure into 4~20mA square root proportional current and transmits it to the distribution box data acquisition module, and the computer in the CEMS cabinet processes the data.
The inner and outer surfaces of the pitot tube are specially treated to effectively avoid flue gas corrosion and reduce dust adhesion. The backflush solenoid valve is mainly used for system backflush when measuring dirty gases (such as flue gas discharged from boilers): when dust and dirt are adhered to and accumulated in the probe detection hole, the solenoid valve is opened at a fixed time or according to a predetermined program, and compressed air is connected to the two pressure pipes at the same time for blowing and removal. During normal measurement, the solenoid valve is in the closed state.
Technical Features
l It can measure the temperature, pressure and flow rate of flue gas in real time, and output it through 3-way analog signal 2-wire 4~20mA.
l Automatically and regularly backflush the dynamic and static pressure ends of the pitot tube.
lHigh measurement accuracy, good reliability, and long-term continuous operation.
lEasy to install and wire, low maintenance.
Technical indicators
ØRange: linear output 0-30m/s;
ØOutput signal: 4~20mA two-wire system;
ØMeasurement accuracy: ±2%FS;
ØCalibration frequency: 12 months;
ØResponse time: <1s;
ØDifferential pressure (temperature, pressure) transmitter power supply: 24VDC, two-wire;
ØOverpressure limit of differential pressure transmitter: 4.0MPa;
Ø Pitot tube material: 304, 316L stainless steel;
Ø Normally closed back-blowing solenoid valve power supply: 220VAC, 50Hz;
Ø Pitot tube insertion length: 500~2000mm optional;
ØPressure transmitter range: -5~+5kPa;
ØTemperature transmitter range: 0~300℃;
Ø Medium temperature range: -40~500℃;
ØAmbient temperature: -40~85℃;
ØStorage temperature: 0~50℃;
ØStorage humidity: 0~85%RH.
ØMounting flange: DN50;
ØMaterial: SUS316L
The difference between conventional CEMS and ultra-low CEMS
Conventional CEMS flue gas online monitoring system parameters and ranges
parameter | Measuring range | method |
SO2 concentration | (0-700) mg/m³ (range can be expanded) | UV differential method |
NO concentration | (0-350) mg/m³ (range can be expanded) | UV differential method |
Flue gas flow rate | (0-40) m/s | S-type Pitot tube differential pressure method |
Oxygen content | (0-25)%vol | Electrochemical method |
Flue gas temperature | (0-400)℃ | PT100 |
Flue gas pressure | (-1000~1000)Pa | Pressure transmitter |
Particles | (0-200) mg/m³ | Laser backscatter |
humidity | (0-40)% | Resistor-capacitor |
Ultra-low cems + ultra-low dust (this model is designed for areas with strict environmental protection requirements, smoke and dust are independent structures)
Ultra-low cems flue gas emission continuous monitoring system
Monitoring parameters and range
parameter | Parameter range | parameter | Parameter range |
Measuring principle | UV differential spectroscopy | Repeatability | ≤0.5% |
Measurement items | SO2, NO, O2 (electrochemical principle) | Warm-up time | 60min |
Range | SO2(0-200)mg/m³ NO(0-130)mg/m³ O2(0-25)mg/m³ | Flow rate | (5-40) m/s |
Linearity error | No more than ±1%FS | temperature | (0-400)℃ |
Zero drift | No more than ±1%FS | pressure | (±10)Pa |
Range drift | No more than ±1%FS | Voltage influence | The analyzer reading does not vary by more than ±2%FS |
Sample gas flow | 1-1.5L/min | Communication interface | RS232, RS485 (support Modbus protocol) |
Ultra-low emission dust monitoring system
Parameters and range
parameter | Parameter range | parameter | Parameter range |
How it works | Laser forward scattering measurement principle | Detection limit | When the full scale value of the analytical instrument is ≤50mg/m³, the detection limit is ≤1.0mg/m³ (no requirement when the full scale value is >50mg/m³) |
Measurement items | Industrial waste gas, smoke | ||
Optical characteristics | Working wavelength (650±20)nm | Measurement conditions | Flue flow rate: (0-30) m/s |
Power supply requirements | AC380V or 220V optional, power 3KW | Flue gas temperature: Maximum 300°C | |
Range | 0-20mg/m³ Other ranges can be customized | Work Environment | Working temperature: -20-+50℃ |
Zero drift | No more than ±1%FS | Interface Characteristics | Analog output (4-20) mA Digital interface: RS485 |
Range drift | No more than ±1%FS | Flow rate | (5-40) m/s range can be customized |
pressure | (±10) Pa range can be customized | temperature | (0-400)℃ range can be customized |
the difference:
1. The specific measurement range of the equipment analyzer is different.
2. The equipment has different parameter measurement methods. For example, ordinary particle measurement is in-situ laser backscattering, while ultra-low particle measurement is extraction laser forward scattering.
3. The analyzer gas chambers are different. The common analyzer has a single gas chamber, while the ultra-low analyzer has a double gas chamber. The range is small, the optical path is long, and the accuracy is higher. The ultra-low analyzer adds a unique prism. The conventional one does not. This makes it more accurate.
The selection of ordinary equipment and ultra-low equipment should be made correctly according to local policy requirements.
Related article
-
Forest fire weather station FT-SL10 helps mountainous areas to better cope with fires
2024-03-14 -
Forest fire weather station, intelligent fire prevention
2024-03-20 -
Odor Online Monitoring - A Solution for Malodor Detection
2024-10-24 -
IoT weather stations help smarten up agriculture
2024-02-27 -
What is an on-farm microclimate monitoring system?
2024-05-15 -
What is the Negative Oxygen Ion Monitoring System?
2024-02-22 -
Four-parameter weather station with four core weather elements
2024-08-05 -
Integrated forest fire risk factor monitoring station component
2024-05-16